一、欠注
成因及對策
1.供料不足。應(yīng)適當(dāng)加大供料量。
2.成型周期太短。應(yīng)適當(dāng)延長。
3.注射壓力偏低。應(yīng)適當(dāng)提高。
4.注射速度太慢。應(yīng)適當(dāng)加快。
5.原料干燥不良。應(yīng)對原料進(jìn)行干燥。
6.料筒或模具溫度太低,流道凍結(jié)過早。應(yīng)適當(dāng)提高料筒或模具溫度,擴(kuò)
大流道截面積,增加注射速度。
7.制品壁太薄。應(yīng)在可能的情況下適當(dāng)加厚。
8.澆注系統(tǒng)結(jié)構(gòu)尺寸偏小。應(yīng)適當(dāng)放大澆口和流道截面。
9.模具排氣不良。應(yīng)增加模具排氣。
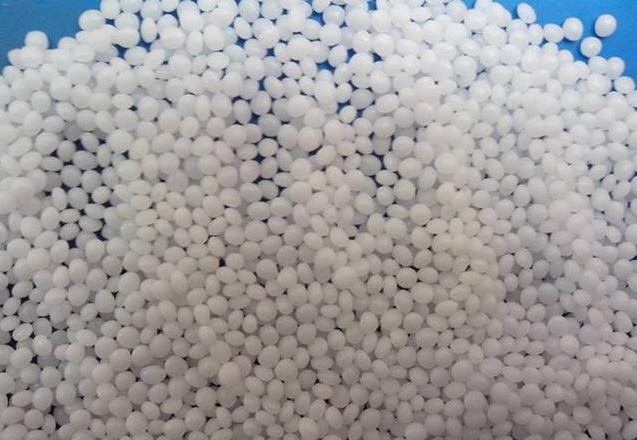
二、溢料飛邊
成因及對策
1.熔料溫度太高。應(yīng)適當(dāng)降低。
2.注射壓力太高。應(yīng)適當(dāng)降低料筒和噴嘴溫度。
3.鎖模力不足。應(yīng)增加鎖模力。
三、真空孔
成因及對策
1.成型溫度太高。應(yīng)適當(dāng)降低。
2.澆口位置設(shè)置不當(dāng)。對于壁厚部位,應(yīng)重新配置澆口。
3.注射壓力偏低。應(yīng)適當(dāng)提高。
4.保壓不足。應(yīng)適當(dāng)延長注射保壓時間。
5.注射速度太慢或太快。應(yīng)根據(jù)具體情況適當(dāng)調(diào)整。
6.模具溫度太高。應(yīng)適當(dāng)降低。
7.射料桿前進(jìn)時間太短。應(yīng)適當(dāng)延長。
8.澆注系統(tǒng)設(shè)計不合理。應(yīng)適當(dāng)放大澆口和流道截面積。
四、氣泡及表面麻點(diǎn)
成因及對策
1.制品冷卻收縮的部分不能由保壓補(bǔ)料所充分彌補(bǔ)時,就會在制品表面產(chǎn)生小孔或氣泡。應(yīng)適當(dāng)提高注射壓力和延長保壓時間。
2.緩沖量不足。應(yīng)適當(dāng)增加。
3.噴嘴溫度太低。應(yīng)適當(dāng)提高。
4.澆口截面尺寸太小。應(yīng)適當(dāng)放大。
5.澆口位置設(shè)置不當(dāng)。對于壁厚部位,應(yīng)重新配置澆口。
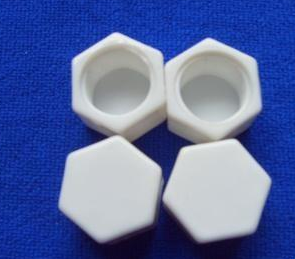
五、縮癟
成因及對策
1.料筒溫度太高。應(yīng)適當(dāng)降低成型溫度。
2.注射壓力偏低。應(yīng)適當(dāng)提高。
3.注射速度太快。應(yīng)適當(dāng)降低。
4.成型周期太短。應(yīng)適當(dāng)延長。
5.保壓時間太短。應(yīng)適當(dāng)延長。
6.澆注系統(tǒng)結(jié)構(gòu)尺寸偏小。應(yīng)適當(dāng)放大澆口和流道截面。
7.澆口位置設(shè)置不當(dāng)。應(yīng)重新定位澆口。
8.供料不足。應(yīng)適當(dāng)增加供料量。
六、空洞及燒焦
成因及對策
1.模具排氣不良型腔中的殘留空氣被熔料包裹,受到絕熱壓縮,形成空洞,周圍的樹脂被燒焦。應(yīng)通過改變澆口位置和增加模具排氣來解決。
2.模具偏芯或偏厚。應(yīng)進(jìn)行修整。
3.注射速度太快。應(yīng)適當(dāng)減慢。
七、熔接痕
成因及對策
1.熔料溫度太低。應(yīng)適當(dāng)提高噴嘴和料筒溫度。
2.注射速度太慢。應(yīng)適當(dāng)加快。
3.澆口截面尺寸太小。應(yīng)適當(dāng)放大。
4.模具溫度太低。應(yīng)適當(dāng)提高。
八、波流痕
成因及對策
1.注射壓力太高。應(yīng)適當(dāng)降低。
2.模具排氣不良。應(yīng)增加模具排氣。
3.澆注系統(tǒng)結(jié)構(gòu)尺寸偏小,流動阻力太大。應(yīng)適當(dāng)放大澆口和流道截面。
九、霜紋
成因及對策
1.料筒溫度太高。應(yīng)適當(dāng)降低成型溫度。
2.模具溫度太低。應(yīng)適當(dāng)提高。
3.注射速度太快。應(yīng)適當(dāng)減慢。
4.原料中水分含量太高。應(yīng)進(jìn)行干燥處理。
十、銀絲及斑紋成因及對策
1.成型工藝條件控制不當(dāng)。應(yīng)適當(dāng)調(diào)整。
2.滯留物的過熱分解導(dǎo)致產(chǎn)生銀絲及斑紋。應(yīng)清除分解的滯留物。
3.料筒或噴嘴局部過熱,導(dǎo)致熔料過熱分解。應(yīng)適當(dāng)降低料筒或噴嘴溫度。
4.注射壓力和注射速度太低或太高都會產(chǎn)生銀絲及斑紋。一般情況下,型腔壓力不足容易產(chǎn)生這種故障。對此,應(yīng)適當(dāng)提高成型和模具溫度,增加熔料的流動性,并適當(dāng)提高注射壓力和延長成型周期。若在型腔壓力較高的條件下產(chǎn)生銀絲及斑紋時,應(yīng)適當(dāng)降低銀注射壓力和注射速度。
5.噴嘴孔徑太小,應(yīng)換用孔徑較大的噴嘴。
6.原料干燥不良。一般情況下,80~90℃條件下干燥3~4小時。
7.澆注系統(tǒng)結(jié)構(gòu)尺寸偏小。應(yīng)適當(dāng)放大澆口和流道截面。
十一、冷料瑕痕
成因及對策
1.產(chǎn)生這一故障的主要原因是由于冷料隨同熔料進(jìn)入型腔,導(dǎo)致澆口附近產(chǎn)生疵點(diǎn)。對此應(yīng)適當(dāng)提高模具溫度,擴(kuò)大澆口截面,改變澆口位置和降低注射速度。
2.在設(shè)計制品的形體結(jié)構(gòu)時,壁厚截面變化太快。應(yīng)平滑過度。
3.澆注系統(tǒng)設(shè)計不當(dāng)。應(yīng)修改設(shè)計,使熔料充模順暢。
十二、表面皺紋
成因及對策
1.產(chǎn)生表面皺紋的較主要原因是模具型腔壓力不足。應(yīng)適當(dāng)提高注射壓力。
2.澆注系統(tǒng)結(jié)構(gòu)尺寸太小。應(yīng)適當(dāng)加大噴嘴、澆口和流道截面,防止壓力損失。
3.模具溫度太低。應(yīng)適當(dāng)提高。
十三、表面波紋
成因及對策
1.表面波紋和表面皺紋較難區(qū)別,所不同點(diǎn)在于波紋是因澆口的噴射現(xiàn)象引起的。因此,應(yīng)適當(dāng)擴(kuò)大澆口截面及減慢注射速度。
2.模具溫度太低。應(yīng)適當(dāng)提高模具溫度,增加充模冷料的流動性能,使?jié)部趪娚洚a(chǎn)生的波紋不留在制品表面。
3.澆口位置設(shè)置不當(dāng)。應(yīng)選擇即使發(fā)生澆口噴射波紋,在外觀上也沒有很大影響的部位設(shè)置澆口,也可采用凸?jié)部谛问健?br>4.注射機(jī)注射量不足也會引起制品產(chǎn)生表面波紋。對此,應(yīng)換用規(guī)格較大的注射機(jī)。
十四、邊緣處產(chǎn)生弧形
成因及對策
1.熔料溫度太低。應(yīng)適當(dāng)提高噴嘴和料筒溫度。
條紋及麻點(diǎn)
2.注射壓力太低。應(yīng)適當(dāng)提高注射壓力和保壓壓力。
3.模具溫度太慢。應(yīng)適當(dāng)提高。
十五、燒焦及變色
成因及對策
1.熔料過熱分解或在料筒內(nèi)滯留時間太長。應(yīng)適當(dāng)降低噴嘴及料筒溫度,或換用小容量注射機(jī)。
2.注射速度太高。應(yīng)適當(dāng)降低。
3.加料過程中,樹脂粒料帶入料筒的空氣排不出來。應(yīng)通過加大背壓,從料斗中排氣。
4.模具排氣不良。應(yīng)增加模具排氣,并適當(dāng)調(diào)整充模速度。
十六、表面污物淀積
成因及對策
1.聚甲醛原料中的添加物污染了模具或微量甲醛氣體與模具接觸后產(chǎn)生了了水,引起制品表面污物淀積。對此,一是合理控制模具溫度、熔料溫度、注射速度以及合理設(shè)置排氣系統(tǒng);二是保持模具清潔,若模腔表面有大量沉積物粘著,可用竹勺、黃銅勺等不易損傷模具的工具鏟刮,也可用專門的MD清潔劑去除。
2.成型工藝條件控制不當(dāng)是產(chǎn)生淀積物的主要原因。成型聚甲醛時,一是注射速度不能太快,否則模腔內(nèi)的氣體不能及時排出,會引起熔料絕熱壓縮,促使淀積物產(chǎn)生;二是模具溫度必須合理控制,若模溫太高或太低都會引起甲醛游離出來形成淀積物;三是熔料溫度不能太高,而熔料在料筒中的滯留時間不能太長,否則會使聚甲醛變化或促使甲醛氣體游離;四是聚甲醛原料必須充分干燥,因?yàn)樗謺偈沟矸e物的產(chǎn)生。
十七、尺寸波動
成因及對策
1.料筒溫度的波動引起制品結(jié)構(gòu)尺寸的變化。應(yīng)穩(wěn)定料筒溫度。
2.緩沖量變化不定引起尺寸波動。應(yīng)使緩沖量保持恒定。
3.模具溫度太低或太高都會導(dǎo)致尺寸波動。應(yīng)準(zhǔn)確控制模溫。
4.注射速度太慢。應(yīng)快速充模。
5.制品冷卻不均勻,引起尺寸不穩(wěn)定。應(yīng)采用退火工藝處理脫模后的制品,制品脫模后仍需均勻冷卻。
6.模具設(shè)計不當(dāng)。對于多腔模具,應(yīng)合理設(shè)計型腔排列形式合澆口尺寸,確保充模同步。
十八、翹曲變形

成因及對策
1.模具溫度不均勻。模溫不均勻會使溫度較高部位制品表面收縮較大,因此,應(yīng)盡量使模溫均勻,并適當(dāng)降低模溫,延長冷卻時間。應(yīng)適當(dāng)提高料筒溫度。
2.成型周期偏短。應(yīng)適當(dāng)延長。
3.注射壓力太低。應(yīng)適當(dāng)提高。
4.冷卻不均勻或冷卻時間太短。制品脫模后可在矯正框中進(jìn)一步冷卻定型。
5.保壓時間偏短。應(yīng)適當(dāng)延長。成型時,注射時間較好比澆口封閉時間略長為好。
6.澆注系統(tǒng)結(jié)構(gòu)設(shè)計不合理,導(dǎo)致充模時熔料流動方向不平行,各部位收縮率差異較大。在選定澆口位置時,應(yīng)使熔料在模腔內(nèi)平行流動,澆口形式較好采用多點(diǎn)式點(diǎn)澆口。
7.制品結(jié)構(gòu)設(shè)計不合理。在設(shè)計制品形體結(jié)構(gòu)時,應(yīng)盡量減少壁厚差異,避免引起較大的收縮差異。在制品的薄弱部位,可設(shè)計一些加強(qiáng)筋,防止收縮變形太大。
8.模具裝配不良。分型面未對中。應(yīng)重新裝配模具。
十九、脆弱破損
成因及對策
1.噴嘴部位溫度太低。應(yīng)適當(dāng)提高噴嘴溫度并清除噴嘴滴涎形成的早凝廢料。
2.成型周期偏短。應(yīng)適當(dāng)延長。
3.注射壓力偏低。應(yīng)適當(dāng)提高。
4.保壓時間太長。應(yīng)適當(dāng)縮短。
5.模具排氣不良。應(yīng)增加模具排氣。
6.原料干燥不良。應(yīng)進(jìn)行預(yù)干燥處理,降低原料中的水分和易揮發(fā)物含量。
7.噴嘴和主流道間有冷料滯留。應(yīng)清除冷料,排除噴嘴處的滴漏現(xiàn)象。
8.由于模具溫度太低,注射壓力過高,以及壁厚不均勻等原因,導(dǎo)致制品內(nèi)集中了大量的殘余應(yīng)力,引起制品脆化。應(yīng)調(diào)整模具溫度、注射壓力及保壓時間,制品壁厚應(yīng)盡量均勻,減少加工殘余應(yīng)力。
9.制品的轉(zhuǎn)角處無過渡圓弧,尖角產(chǎn)生應(yīng)力集中,導(dǎo)致制品脆化破損。在設(shè)計制品時,要減少尖角,圓滑過渡;在成型過程中,要防止產(chǎn)生毛刺。
10.熔料過熱分解導(dǎo)致制品脆化。應(yīng)降低過熱部位的溫度。
11.原料中混入雜質(zhì)異物,應(yīng)清除原料中雜質(zhì)異物,拆卸和清洗螺筒及噴嘴,并檢查原料中再生料回用比例是否太高,適當(dāng)減少其用量。
二十、粘模芯
成因及對策
1.注射壓力太高。應(yīng)適當(dāng)降低。
2.注射保壓時間太長。應(yīng)適當(dāng)縮短。
3.模具脫模斜度太小。應(yīng)適當(dāng)增加。
4.模具閉合時間太長。應(yīng)適當(dāng)縮短。
5.模芯處溫度太高。應(yīng)適當(dāng)降低。
6.澆口位置不當(dāng),應(yīng)設(shè)置在壁厚處。
7.注射機(jī)規(guī)格太小。應(yīng)選用較大規(guī)格的注射機(jī)。
8.墊料太多。應(yīng)適當(dāng)減少墊料。
二十一、粘模腔
成因及對策
1.墊料太多。應(yīng)適當(dāng)減少墊料。
2.注射壓力太高。應(yīng)適當(dāng)降低。
3.螺桿轉(zhuǎn)速太低。應(yīng)適當(dāng)提高。
4.螺桿前進(jìn)時間太長。應(yīng)適當(dāng)縮短。
5.模具溫度太高。應(yīng)適當(dāng)降低。
6.注射背壓不足。應(yīng)適當(dāng)提高。
7.模具閉合太快。應(yīng)適當(dāng)延長模具閉合時間。
8.脫模斜度太小。應(yīng)適當(dāng)增加。
無錫嘉弘塑料科技有限公司可根據(jù)客戶要求染色加工ABS、PS、PC、PC/ABS、PP等工程塑料粒子;各種填充、阻燃、增強(qiáng)改性ABS、PP、PC/ABS、PA等工程塑料粒子;各種汽車門板、保險杠、儀表板、發(fā)動機(jī)蓋板、車燈等汽車專用料。
無錫嘉弘塑料科技有限公司擁有近30年P(guān)VC粒料的研發(fā)、造粒生產(chǎn)經(jīng)驗(yàn),改性工程塑料的研發(fā)和生產(chǎn)經(jīng)驗(yàn);專業(yè)技術(shù)服務(wù)團(tuán)隊可為客戶提供一站式改性塑料系統(tǒng)解決方案。如想了解更多關(guān)于產(chǎn)品的信息,歡迎登錄我們的官網(wǎng)∶www。js-plastics。com,咨詢在線客服或撥打熱線。固話:0510-68755207 手機(jī):15190220696,我們將竭誠為您服務(wù)。
(免責(zé)聲明: 本站內(nèi)收錄的所有教程與資源均來自于互聯(lián)網(wǎng),其版權(quán)均歸原作者及其網(wǎng)站所有,本站雖力求保存原有的版權(quán)信息,但由于諸多原因,可能導(dǎo)致無法確定其真實(shí)來源,請原作者原諒!如果您對本站教程與資源的歸屬存有異議,請立即通知小編,情況屬實(shí),我們會盡快予以刪除。)